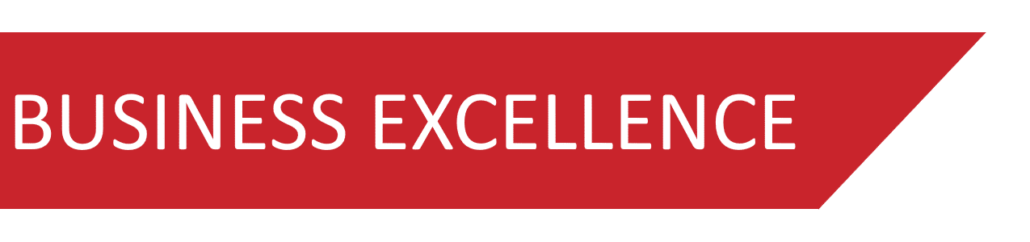
At Merit, we incorporate additional value into every interaction across our organization. This means prioritizing business excellence each step of the way. From innovating high-quality products to providing exceptional customer service, we go above and beyond to show our healthcare partners our commitment to ongoing superior performance.
One aspect of our business excellence strategy is incorporating vertical integration into our processes wherever possible. Merit strives to own the company supply chain to minimize disruptions, maintain closer control over operations, and ultimately, ensure product reaches physicians to serve patients—when they need it.
We sat down with John Hall, Executive VP of Advanced Materials Technologies at Merit, to chat about how moving the process of making ePTFE in-house helps us supply physicians with the HeRO® Graft.
To help our readers understand, what is ePTFE and how is it used in medical products?
EPTFE, or expanded polytetrafluoroethylene, acts like the material of a rain jacket. It allows water vapor to pass through while remaining resistant to liquid water. The result is a breathable, tightly porous product.
Researchers discovered that ePTFE is also an excellent replacement for blood vessels in the body, as it’s inert and biocompatible. This ensures it can be implanted without significant inflammatory response. For these reasons, ePTFE is used to increase the performance of several Merit products, including the HeRO Graft.
What role does the HeRO Graft serve in treating patients?
The HeRO Graft provides hemodialysis access for patients with renal disease who are catheter-dependent or approaching catheter dependency due to the blockage of veins leading to the heart.
These patients deserve comfort and convenience to live their lives to the fullest. The HeRO Graft helps by reducing infection and improving dialysis adequacy. Because the HeRO Graft is implanted inside the body, it requires a material like ePTFE to be biocompatible.
Why did Merit decide to vertically integrate the production of ePTFE?
Six or seven years ago, we were outsourcing our supply of ePTFE through another company. Merit’s Chairman and CEO, Fred Lampropoulos, envisioned bringing production in-house in the event that supply chain disruptions interfere with our ability to provide this important product to patients in need.
As it turns out, during the process of starting our own production of the material, we did face a disruption. Thankfully, due to Fred’s foresight, we were able to continue manufacturing the HeRO Graft and other products using ePTFE.
Quality control was another major factor in our decision. When we’re the ones creating the material, we can more closely monitor output, helping to produce a superior product for patients.
How does this benefit our healthcare partners and their patients?
Bringing this process in-house allows us to deliver our products in a timelier manner—critical when you’re in the business of saving lives.
Producing our own ePTFE also allows us to innovate other products where the material could benefit the patient experience.
Discover more of our business excellence strategies, and learn how else we put our healthcare partners and their patients first.